수축공의 가장 기본적인 원인은 알루미늄 합금이 액체 속에서 수축 응고할 때 실리카졸 정밀주조 공장에서 주조물의 특정 위치(보통 최종 응고가 최종적으로 응고되는 핫스팟)에서 액체를 얻을 수 없다는 것을 발견한 것입니다. 시간에 맞춰 금속을 공급하므로 그 시점에 수축 공동이 생성됩니다.
초경 알루미늄 합금이나 응고 온도 범위가 좁은 알루미늄 합금의 경우 주조 시 집중 수축 공동이 발생하기 쉽습니다. 합금 조성이 일정대로 진행되면 수축 공동은 일반적으로 주조의 두께가 고르지 않고, 열간 조인트가 너무 많으며, 주입 라이저 제어 시스템이 너무 크고 불합리하게 설계되어 순차적 응고에 도움이 되지 않아 발생합니다. 실리카졸 정밀주조 부품의 열간 접합부는 용탕으로 채워질 수 없습니다. 또는 붓는 온도가 너무 높습니다.
피해야 할 대책:
1: 균일한 두께를 보장하고, 열 접합을 줄이거나, 규칙적인 응고에 도움이 되는 두께 변화를 만들기 위해 주조 구조를 개선합니다.
2: 주문이 동결되도록 라이저 시스템을 효과적으로 설정합니다. 여러 핫스팟이 있는 복잡한 부품의 타설 라이저 시스템에 더 많은 고려가 필요합니다.
3: 부분적인 열 방출의 어려움을 피하기 위해 실리카 졸 정밀 주조 부품 아래에 일정한 거리가 있도록 모듈을 효과적으로 조립하십시오.
4: 쉘 및 용융 금속의 주입 온도가 적합해야 하며 주입 온도가 너무 높지 않아야 합니다.
5: 부을 때 스프루와 라이저에 용융 금속이 채워져 있는지 확인하고 스프루 컵과 라이저에 가열제와 단열제를 추가합니다.
6: 제련 및 가공 기술을 개선하고, 용융 금속의 폐가스 및 금속 산화물을 줄이고, 순환 및 공급 수준을 향상시킵니다.
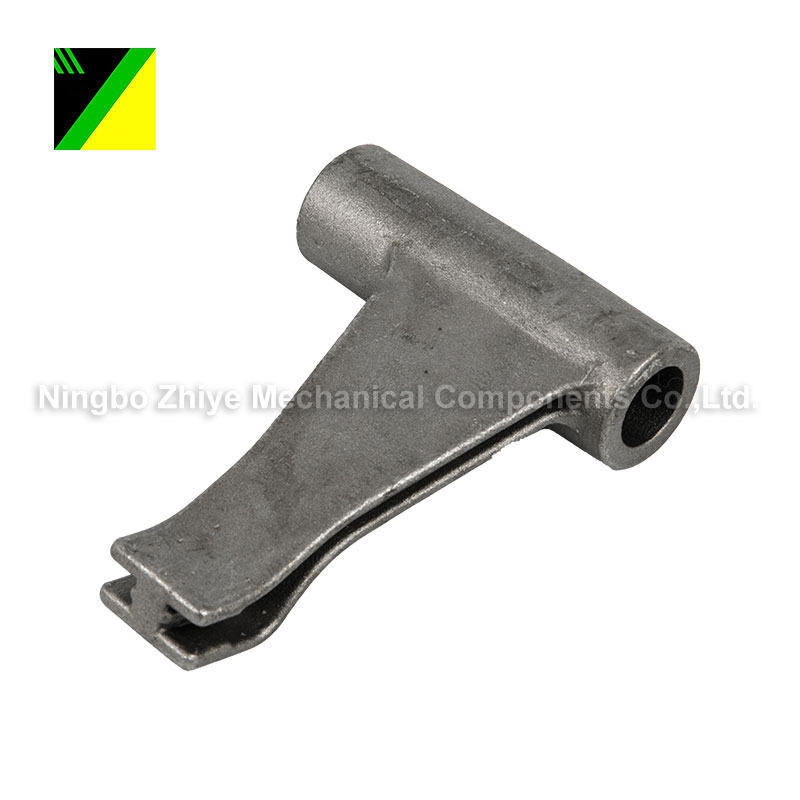